Intelligent virtual assistant to support agile manufacturing teams
This solution will help your employees get better and optimize your daily production at the speed of voice with an intelligent virtual assistant. Powered by artificial intelligence, its knowledge management capabilities allow it to detect best practices, share capitalized knowledge, solve issues and suggest proactive actions.
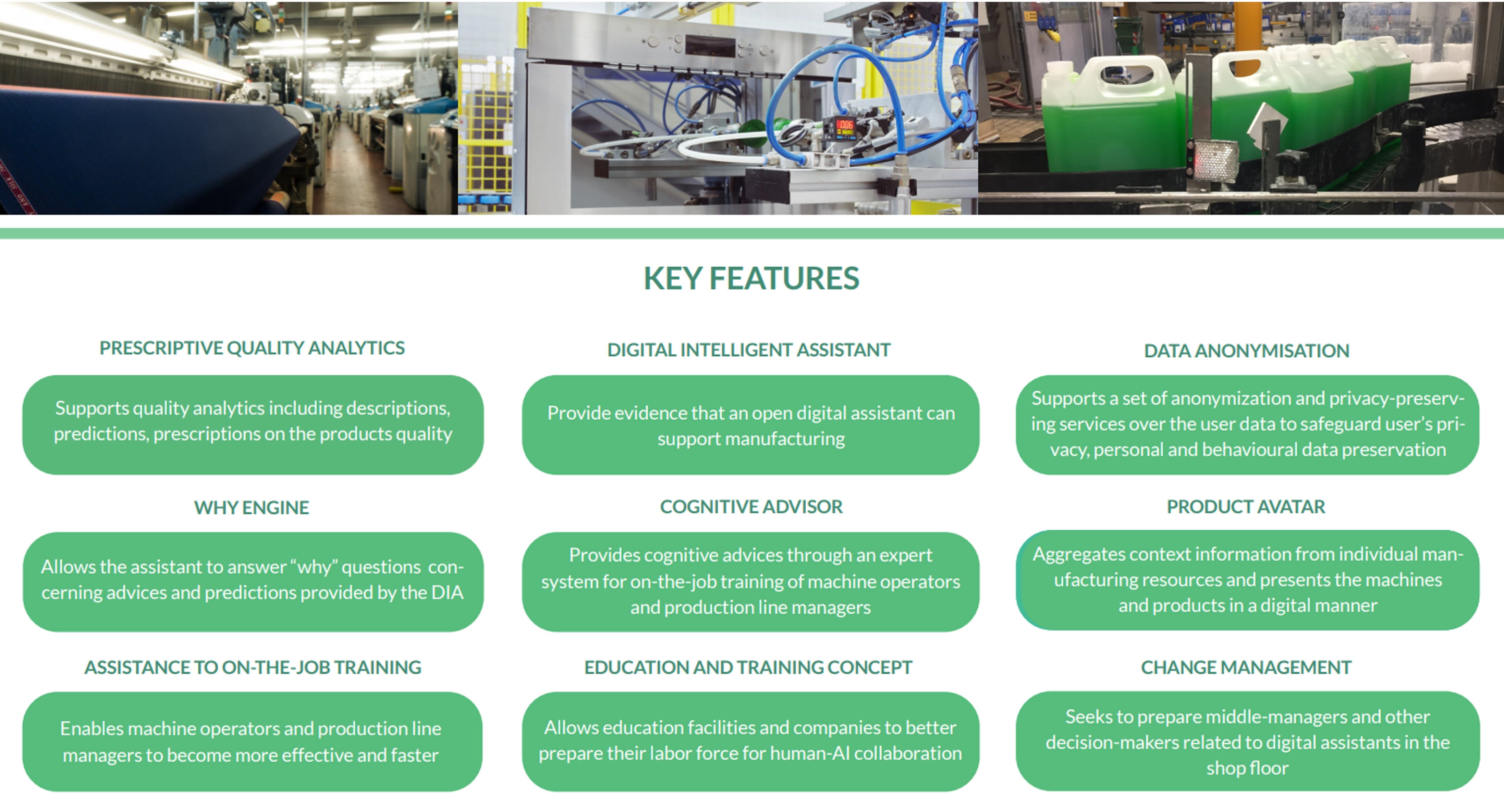
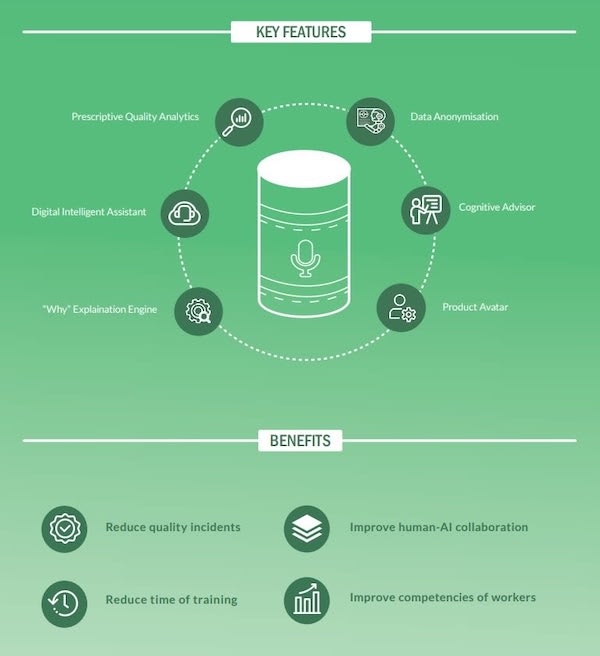
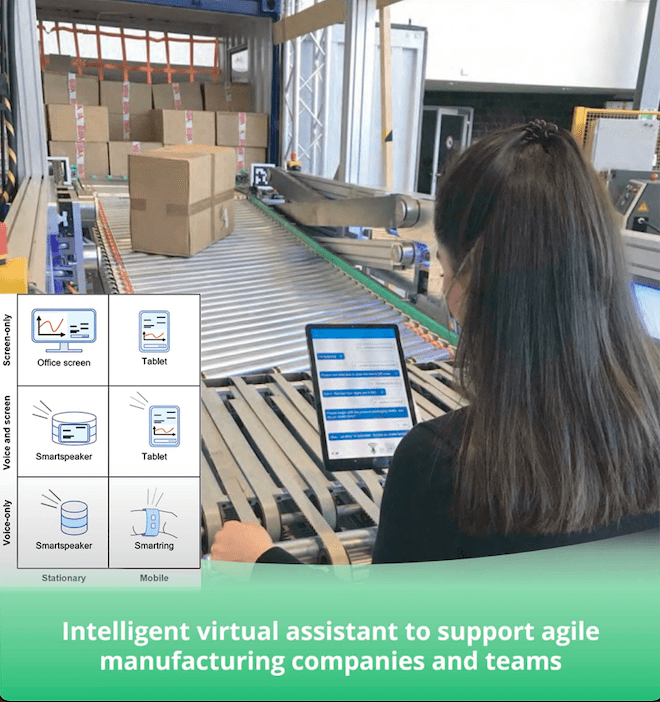
Issue
All companies are facing various challenges to remain competitive, such as: an increasing need for agile production, mass customization, increased expectations for reliability.
Because of these challenges, operators and managers employed in industries where activities are too knowledge-intensive to be automated experience an increased cognitive load, time pressure and no tolerance for quality issues.
This result in many problems, including:
To date, there are no solutions that fully address all these issues.
Because of these challenges, operators and managers employed in industries where activities are too knowledge-intensive to be automated experience an increased cognitive load, time pressure and no tolerance for quality issues.
This result in many problems, including:
- Shortage of skilled labor: Significant time and costs invested in new workers' training, along with the loss of knowledge induced by experienced workers' departure and the loss of production.
- Inefficient production changeover: Smaller production batches with more frequent and complex changeover times, inherent to dynamic production.
- Too high quality cost: Increasing product variability results in quality control complexity, with longer and brand or model dependent checklists and quality issues.
To date, there are no solutions that fully address all these issues.
Solution
Our solution is an intuitive digital assistant for the manufacturing sector that assists operators and managers in daily production.
Equipped with headphones and tablets, users can request status information, predictions and advices with their natural voice or with a mobile device. The entire solution can be fully integrated in the Information System of the plant.
Typical use cases:
Equipped with headphones and tablets, users can request status information, predictions and advices with their natural voice or with a mobile device. The entire solution can be fully integrated in the Information System of the plant.
Typical use cases:
- Process optimization: provides advanced analytics (descriptive, predictive, prescriptive), proactive notifications, suggests process improvements based on historical and real-time data and supports root cause analysis of issues.
- On-the-job training: records best practices, learns how experts solve problems and uses this knowledge to advise novices, reducing training time and cost.
- Operator support: guides users in regular actions and assists in solving problems, providing explanations on given advices. It provides centralized access to production and quality software: stored documents, videos, and recording of information.