Sub-micron engineering for organic powders
New submicronization process compatible with organic compounds that increases their activity (active surface), and allows their co-crystallization or the coating of fragile compounds at the submicron scale.
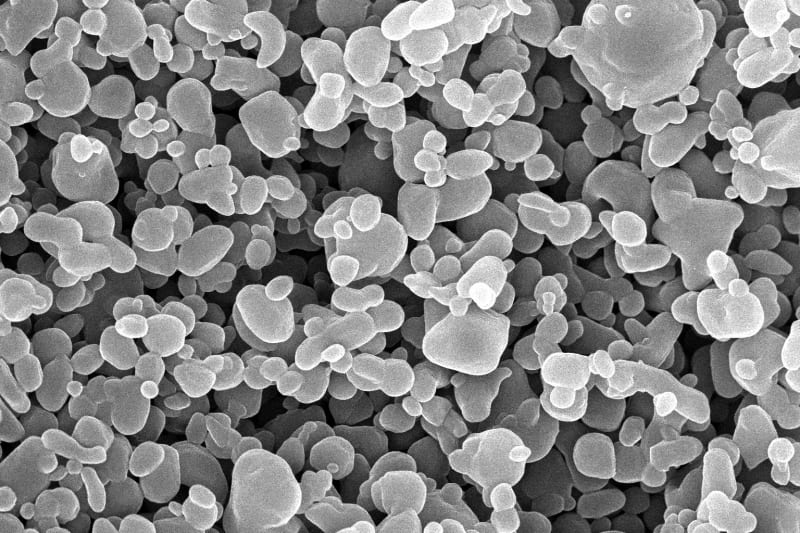
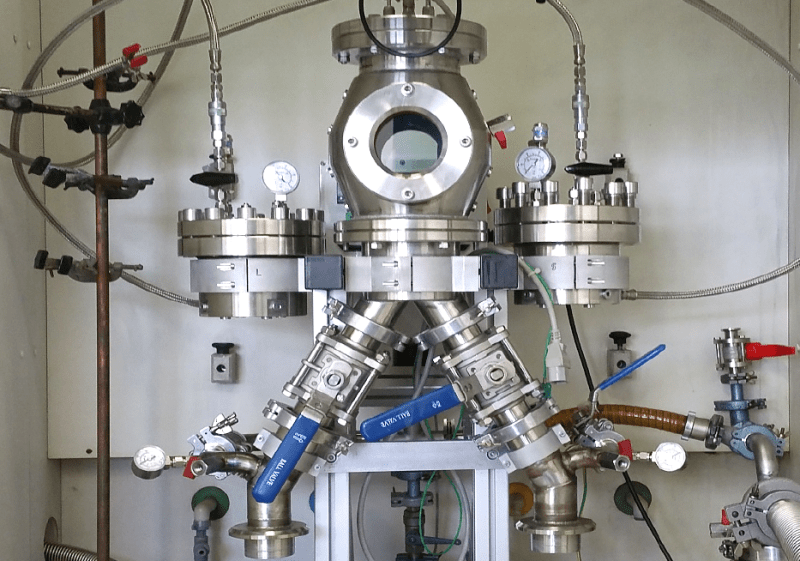
Benefits
- Increased particle reactivity
- Homogenization of particle size
- Possibility of increasing solubility
- Possibility of co-crystallization on a submicron scale
- Possibility of coating fragile compounds on a submicron scale
Issue
Powder compounds are used in the formulation of products for numerous applications such as pharmaceutical, cosmetics, food, ink, pneumatics, etc.
Reducing the size of these compounds (<1μm) can increase their activity (larger active area). Current submicronization techniques are not compatible for organic compounds because of their fragility: high pressure/temperature induced by spray drying, homogenization or grinding.
There are bottom-up submicronization techniques suitable for organic compounds (precipitation, vaporisation, polymerisation, laser ablation) but they are limited to small batch volumes incompatible with industrial production.
Moreover, it is not possible, for example, to co-crystallize on a submicron scale or to coat fragile compounds in industrial proportions.
Solution
We have developed a new Flash Spray Evaporation (SFE) process. It consists of an ultra-fine continuous atomization of the dissolved compound. This process is repeatable and works with a wide range of solvents, allowing the transformation of compounds with low solubility in some solvents.
The resulting particlesare crystalline, smaller than microns in size and have a larger active surface. Their size is controlled and larger at 100nm to avoid nano classification if necessary.
The process has already been proven on an industrial scale for pharmaceutical and cosmetic applications...:
- Submicronization of resveratrol and vanillin to optimize their bioavailability
- Co-crystallization of coffee and glutaric acid
The main differences with current micronization techniques are:
- Fewer pressure stresses than ball crushing and no residue
- Less temperature rise than spray drying
- Finer than air-jet grinding